Technology Trends in the Future of Manufacturing
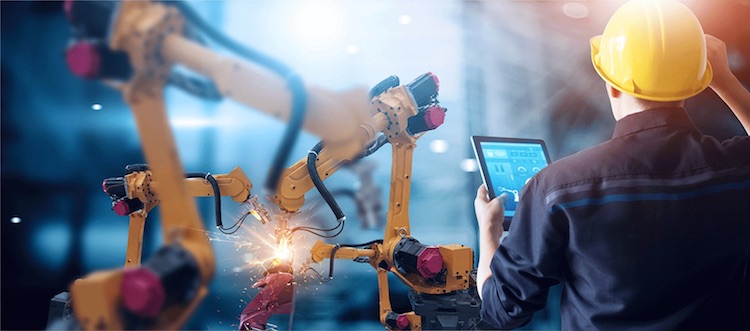
The future of manufacturing is irrevocably bound to technology. “Cheaper, more capable, and more flexible technologies are accelerating the growth of fully automated production facilities,” a McKinsey & Company article explains. Already, robotics, digital twin technology, and the industrial internet of things (IIoT), among other trends, are driving best practices in the manufacturing industry and significantly shaping the future direction of manufacturing.
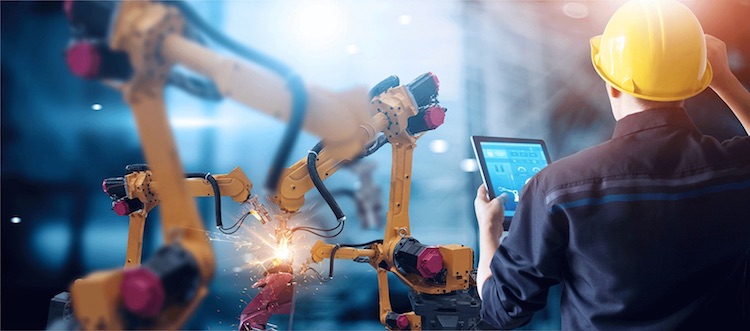
As technology shifts aspects of manufacturing, the roles of project managers and other business professionals will need to evolve as well. In particular, advanced skills in business administration — with a focus on communication, intricate knowledge of processes, and the implementation of new technologies in business settings — will help professionals bridge the gap between new technology trends and the implementation of such technologies in their companies.
Businesses rely on professionals who can help them adopt new tech and keep their manufacturing at the industry forefront. Manufacturing companies seek candidates who have these abilities, potentially leading to roles such as director of operations, financial analyst, business manager, and operations controller.
For professionals considering a career in manufacturing, the following manufacturing trends are impacting both the industry today and the future of manufacturing. A degree such as an online Master of Business Administration can help elevate any professional’s working knowledge of these trends and equip him or her with actionable skills capable of increasing success potential not only for the professional but also for the company for which he or she works.
Trends in the Future of Manufacturing
For professionals to succeed in the future of manufacturing, they will need to understand several current manufacturing trends, such as robotics, digital twin technology, and IIoT. These trends can inform current best practices and also predict future manufacturing directions, alerting professionals to how they may prepare for and adapt to such changes to remain successful in the industry.
Robotics
Advancing technology in robotics is predicted to significantly change the future of manufacturing. Already, collaborative robotics and artificial intelligence (AI) can reduce production costs, increase operational efficiency, and complete menial tasks, thereby creating more time and flexibility for manufacturing professionals to manage production. Additionally, as noted by a Barron’s article, robotics can “bring jobs back to the U.S., improve factory productivity, and help manufacturers adapt to changing consumer preferences.”
As advanced robotics becomes a part of commonplace manufacturing practices, those overseeing the processes will need certain skills to succeed. Managers and business professionals looking to adapt to these changes will need extensive knowledge of management techniques. As technology becomes more advanced, so too should how professionals are prepared to deal with these cutting-edge systems and how they may impact manufacturing spaces.
Digital Twins
A manufacturing trend making waves in the industry is digital twin technology, the process of “digitally modeling the performance of a physical asset or process,” as a Global Manufacturing article explains. The technology is very useful in product development, as it allows virtual simulations that help with development or improvement of new products. It can also help to optimize a company’s supply chain, by providing a clearer view of materials’ usage automating the replenishment process.
While the digital twin concept has been around awhile, implementation has been slow. Now, 50% of large industrial complexes are anticipated to implement the technology by 2021. According to the Global Manufacturing article, digital twin technology is “driving more demand for such capabilities among industrial software vendors.”
One of the reasons why widespread adoption of digital twin tech has been slow is the four-fold necessity of the technology: big data collection, big data management capabilities, AI, and adaptive analytics. Despite the initial challenges the technology entails, companies that do invest in digital twin technology may see a “30% improvement in cycle times of critical processes,” as noted by the Global Manufacturing article. Not only does digital twin tech have the potential to improve processes, predict and prevent machine maintenance, and prolong product life, but it is also expected to bring forth previously unknown collaboration opportunities. Business professionals and managers working with digital twin technology will need extensive knowledge of system processes, technology implementation, and collaborative communication practices.
Industrial Internet of Things (IIoT)
Another manufacturing trend gaining momentum is the industrial internet of things, which refers to the manufacturing industry’s use of interconnected devices in tandem with industrial-level applications. While IIoT comprises countless devices and instruments, a common one is the use of interlinked sensors. Connected sensors in manufacturing offer many unique benefits across the supply chain, including automating inventory management, self-optimization, and collecting valuable data for insight into the production process, to name a few.
As noted in a Digital Lumens article, IIoT solutions “automate manual tasks while delivering new data insights, which can help increase savings, streamline processes, and more.” Some advanced IIoT technologies can already provide insights related to facility energy usage, environmental conditions, and occupancy trends, for example. Facility managers and manufacturing professionals who are focused on maintaining safe, productive, and cost-efficient facilities may gain a lot from acquiring IIoT knowledge and deciding to choose integration for the future of manufacturing at their companies.
Help Shape Future Manufacturing Trends
Manufacturing trends are constantly shifting and evolving, and so too should the skill sets of business professionals. Advanced education programs, such as Maryville University’s online MBA, allow professionals to elevate their understanding of technological processes, management techniques, and collaborative communication strategies that will serve them along the path to success. The future of manufacturing is nearly here; now is the time to move forward.
Sources
Barron’s, “What Robots Mean for the Future of American Manufacturing”
Digital Lumens, “How Can the Industrial Internet of Things (IIoT) Help Facility Management?”
Manufacturing Guide for Mechanical Product Development
Maryville University, Master of Business Administration
Maryville University, Online Business Degrees
McKinsey & Company, “Automation, Robotics, and the Factory of the Future”